Машина за рязане с диамантена тел от силициев карбид, обработка на SiC блокове 4/6/8/12 инча
Принцип на работа:
1. Фиксиране на слитъци: Слитъкът от SiC (4H/6H-SiC) се фиксира върху платформата за рязане чрез приспособление, за да се осигури точност на позициониране (±0,02 мм).
2. Движение на диамантената линия: диамантената линия (галванизирани диамантени частици на повърхността) се задвижва от системата с направляващи колела за високоскоростна циркулация (скорост на линията 10~30 м/с).
3. Подаване при рязане: слитъкът се подава по зададената посока, а диамантената линия се реже едновременно с множество успоредни линии (100~500 линии), за да се образуват множество пластини.
4. Охлаждане и отстраняване на стружки: Напръскайте охлаждаща течност (дейонизирана вода + добавки) в зоната на рязане, за да намалите топлинните повреди и да отстраните стружките.
Ключови параметри:
1. Скорост на рязане: 0,2~1,0 мм/мин (в зависимост от посоката на кристала и дебелината на SiC).
2. Опъване на кордата: 20~50N (твърде високото лесно скъсва кордата, твърде ниското влияе върху точността на рязане).
3. Дебелина на пластината: стандартна 350~500μm, пластината може да достигне 100μm.
Основни характеристики:
(1) Точност на рязане
Толеранс на дебелина: ±5μm (@350μm пластина), по-добър от конвенционалното рязане с хоросан (±20μm).
Грапавост на повърхността: Ra <0,5 μm (не е необходимо допълнително шлайфане, за да се намали количеството последваща обработка).
Изкривяване: <10μm (намалява трудността при последващо полиране).
(2) Ефективност на обработката
Многолинейно рязане: рязане на 100~500 броя наведнъж, увеличавайки производствения капацитет 3~5 пъти (в сравнение с еднолинейно рязане).
Живот на линията: Диамантената линия може да реже 100~300 км SiC (в зависимост от твърдостта на слитъка и оптимизацията на процеса).
(3) Обработка с ниски щети
Счупване на ръбовете: <15μm (традиционно рязане >50μm), подобрява добива на пластината.
Подповърхностен увреден слой: <5μm (намалява отстраняването на полиране).
(4) Опазване на околната среда и икономика
Без замърсяване на строителния разтвор: Намалени разходи за изхвърляне на отпадъчни течности в сравнение с рязането на строителния разтвор.
Използване на материала: Загуба при рязане <100μm/остър, спестяване на SiC суровини.
Режещ ефект:
1. Качество на пластината: без макроскопични пукнатини по повърхността, малко микроскопични дефекти (контролируемо удължаване на дислокациите). Може директно да влезе в звено за грубо полиране, скъсявайки технологичния процес.
2. Консистенция: отклонението в дебелината на пластината в партидата е <±3%, подходящо за автоматизирано производство.
3. Приложимост: Поддържа рязане на блокове 4H/6H-SiC, съвместимо с проводим/полуизолиран тип.
Техническа спецификация:
Спецификация | Детайли |
Размери (Д × Ш × В) | 2500x2300x2500 или персонализиране |
Диапазон на размерите на обработваемия материал | 4, 6, 8, 10, 12 инча силициев карбид |
Грапавост на повърхността | Ra≤0,3u |
Средна скорост на рязане | 0,3 мм/мин |
Тегло | 5,5 тона |
Стъпки за настройка на процеса на рязане | ≤30 стъпки |
Шум от оборудването | ≤80 dB |
Опъване на стоманена тел | 0~110N (0,25 опъване на телта е 45N) |
Скорост на стоманена тел | 0~30 м/с |
Обща мощност | 50 кВт |
Диаметър на диамантеното въже | ≥0,18 мм |
Крайна плоскост | ≤0,05 мм |
Скорост на рязане и чупене | ≤1% (с изключение на човешки причини, силициев материал, линия, поддръжка и други причини) |
Услуги на XKH:
XKH предоставя цялостно обслужване на машина за рязане с диамантена тел от силициев карбид, включително избор на оборудване (съответствие между диаметъра и скоростта на телта), разработване на процеса (оптимизиране на параметрите на рязане), доставка на консумативи (диамантена тел, водещо колело) и следпродажбено обслужване (поддръжка на оборудването, анализ на качеството на рязане), за да помогне на клиентите да постигнат висок добив (>95%), нискобюджетно масово производство на SiC пластини. Също така предлага персонализирани подобрения (като ултратънко рязане, автоматизирано зареждане и разтоварване) с време за изпълнение от 4 до 8 седмици.
Подробна диаграма
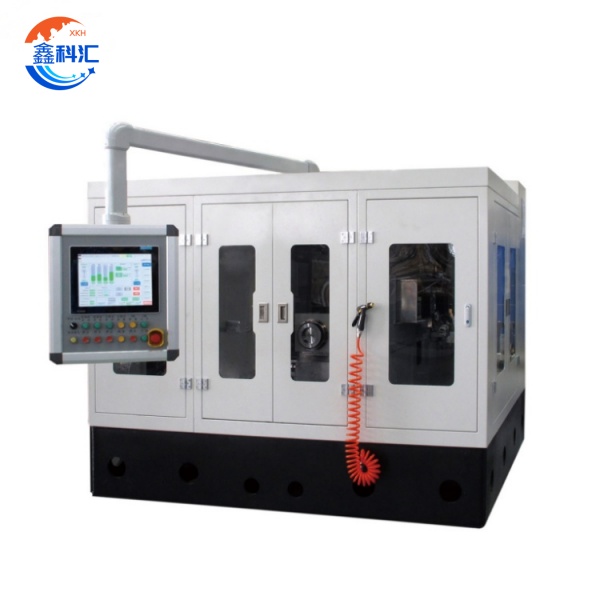
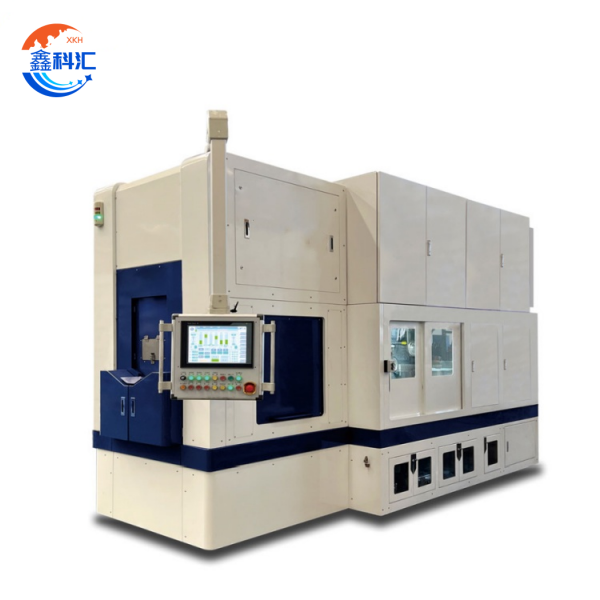
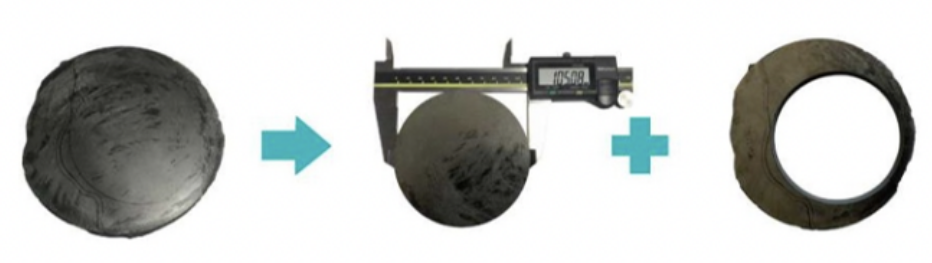