Технологията за нарязване на пластини, като критична стъпка в процеса на производство на полупроводници, е пряко свързана с производителността, добива и производствените разходи на чипа.
#01 Предистория и значение на нарязването на вафли
1.1 Определение за нарязване на вафли
Нарязването на пластини (известно още като скрайбиране) е съществена стъпка в производството на полупроводници, насочена към разделянето на обработените пластини на множество отделни кристали. Тези кристали обикновено съдържат пълна функционалност на схемата и са основните компоненти, използвани в крайна сметка в производството на електронни устройства. Тъй като дизайнът на чиповете става все по-сложен и размерите продължават да се свиват, изискванията за прецизност и ефективност на технологията за нарязване на пластини стават все по-строги.
В практическите операции, нарязването на пластини обикновено използва високопрецизни инструменти, като например диамантени дискове, за да се гарантира, че всяка матрица остава непокътната и напълно функционална. Ключовите стъпки включват подготовка преди рязане, прецизен контрол по време на процеса на рязане и проверка на качеството след рязане.
Преди рязане, пластината трябва да бъде маркирана и позиционирана, за да се осигурят точни траектории на рязане. По време на рязане, параметри като налягане на инструмента и скорост трябва да бъдат стриктно контролирани, за да се предотврати повреда на пластината. След рязане се извършват цялостни проверки на качеството, за да се гарантира, че всеки чип отговаря на стандартите за производителност.
Основните принципи на технологията за нарязване на пластини обхващат не само избора на оборудване за рязане и задаването на параметрите на процеса, но и влиянието на механичните свойства и характеристики на материалите върху качеството на рязане. Например, силициевите пластини с ниско диелектрично съотношение (low-k), поради по-ниските си механични свойства, са силно податливи на концентрация на напрежение по време на рязане, което води до повреди като отчупване и напукване. Ниската твърдост и крехкост на материалите с ниско съотношение (low-k) ги правят по-податливи на структурни повреди при механично натоварване или термично напрежение, особено по време на рязане. Контактът между инструмента и повърхността на пластината, съчетан с високи температури, може допълнително да влоши концентрацията на напрежение.
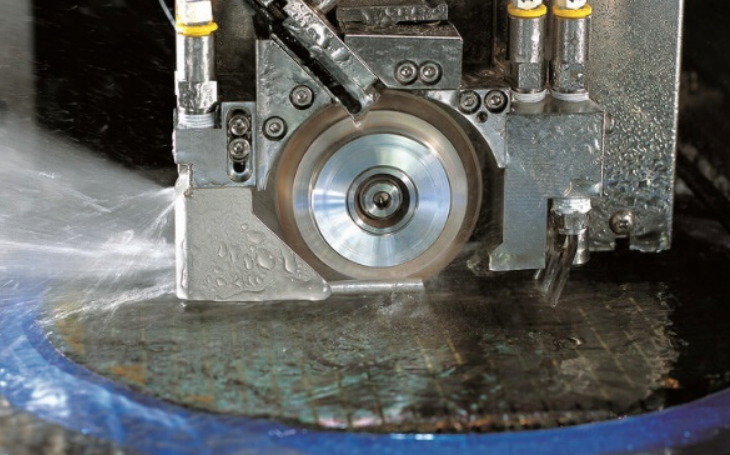
С напредъка в материалознанието, технологията за нарязване на пластини се разшири отвъд традиционните силициеви полупроводници, за да включи нови материали като галиев нитрид (GaN). Тези нови материали, поради своята твърдост и структурни свойства, поставят нови предизвикателства пред процесите на нарязване, изисквайки допълнителни подобрения в инструментите и техниките за рязане.
Като критичен процес в полупроводниковата индустрия, нарязването на пластини продължава да се оптимизира в отговор на променящите се изисквания и технологичния напредък, полагайки основите за бъдещата микроелектроника и технологиите за интегрални схеми.
Подобренията в технологията за нарязване на пластини надхвърлят разработването на спомагателни материали и инструменти. Те обхващат и оптимизация на процесите, подобрения в производителността на оборудването и прецизен контрол на параметрите на нарязване. Тези подобрения целят да осигурят висока прецизност, ефективност и стабилност в процеса на нарязване на пластини, отговаряйки на нуждите на полупроводниковата индустрия за по-малки размери, по-висока интеграция и по-сложни чип структури.
зона за подобрения | Специфични мерки | Ефекти |
Оптимизация на процесите | - Подобряване на първоначалната подготовка, като например по-точно позициониране на пластините и планиране на пътя. | - Намалете грешките при рязане и подобрете стабилността. |
- Минимизиране на грешките при рязане и подобряване на стабилността. | - Приемете механизми за наблюдение и обратна връзка в реално време, за да регулирате налягането, скоростта и температурата на инструмента. | |
- Намаляване на процента на счупване на пластините и подобряване на качеството на чипа. | ||
Подобряване на производителността на оборудването | - Използвайте високопрецизни механични системи и усъвършенствана технология за автоматизирано управление. | - Подобрява точността на рязане и намалява разхищението на материал. |
- Въвеждане на технология за лазерно рязане, подходяща за пластини от високотвърди материали. | - Подобряване на производствената ефективност и намаляване на ръчните грешки. | |
- Увеличете автоматизацията на оборудването за автоматично наблюдение и настройки. | ||
Прецизен контрол на параметрите | - Фино настройване на параметри като дълбочина на рязане, скорост, вид инструмент и методи на охлаждане. | - Осигурете целостта на кристала и електрическите характеристики. |
- Персонализиране на параметри въз основа на материала, дебелината и структурата на пластината. | - Увеличаване на добива, намаляване на разхищението на материали и по-ниски производствени разходи. | |
Стратегическо значение | - Непрекъснато проучване на нови технологични пътища, оптимизиране на процесите и подобряване на възможностите на оборудването, за да се отговори на пазарните изисквания. | - Подобряване на добива и производителността при производството на чипове, подпомагане на разработването на нови материали и усъвършенствани дизайни на чипове. |
1.2 Значението на нарязването на вафли
Нарязването на пластини играе ключова роля в процеса на производство на полупроводници, като пряко влияе върху последващите стъпки, както и върху качеството и производителността на крайния продукт. Неговото значение може да бъде описано подробно, както следва:
Първо, точността и постоянството на нарязването са ключови за осигуряване на добива и надеждността на чипа. По време на производството, пластините преминават през множество стъпки на обработка, за да образуват множество сложни схемни структури, които трябва да бъдат прецизно разделени на отделни чипове (диски). Ако има значителни грешки в подравняването или рязането по време на процеса на нарязване, схемите могат да бъдат повредени, което да повлияе на функционалността и надеждността на чипа. Следователно, високопрецизната технология за нарязване не само гарантира целостта на всеки чип, но и предотвратява повреда на вътрешните схеми, подобрявайки общия процент на добив.
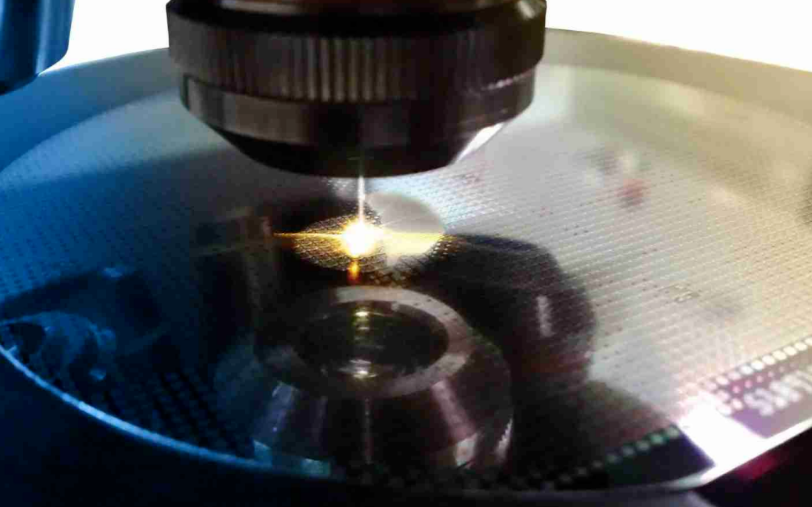
Второ, нарязването на вафли има значително влияние върху ефективността на производството и контрола на разходите. Като ключова стъпка в производствения процес, нейната ефективност пряко влияе върху напредъка на следващите стъпки. Чрез оптимизиране на процеса на нарязване, повишаване на нивата на автоматизация и подобряване на скоростта на рязане, общата ефективност на производството може да бъде значително подобрена.
От друга страна, разхищението на материал по време на нарязването е критичен фактор за управление на разходите. Използването на усъвършенствани технологии за нарязване не само намалява ненужните загуби на материал по време на процеса на рязане, но и увеличава използването на пластините, като по този начин намалява производствените разходи.
С напредъка в полупроводниковите технологии, диаметрите на пластините продължават да се увеличават, а плътността на схемите съответно се увеличава, което поставя по-високи изисквания към технологията за нарязване. По-големите пластини изискват по-прецизен контрол на пътищата на рязане, особено в области с висока плътност на схемите, където дори малки отклонения могат да доведат до дефектиране на множество чипове. Освен това, по-големите пластини включват повече линии на рязане и по-сложни технологични стъпки, което налага допълнителни подобрения в прецизността, последователността и ефективността на технологиите за нарязване, за да се справят с тези предизвикателства.
1.3 Процес на нарязване на вафли
Процесът на нарязване на вафли обхваща всички стъпки - от фазата на подготовка до крайната проверка на качеството, като всеки етап е от решаващо значение за осигуряване на качеството и производителността на нарязаните чипсове. По-долу е дадено подробно обяснение на всеки етап.
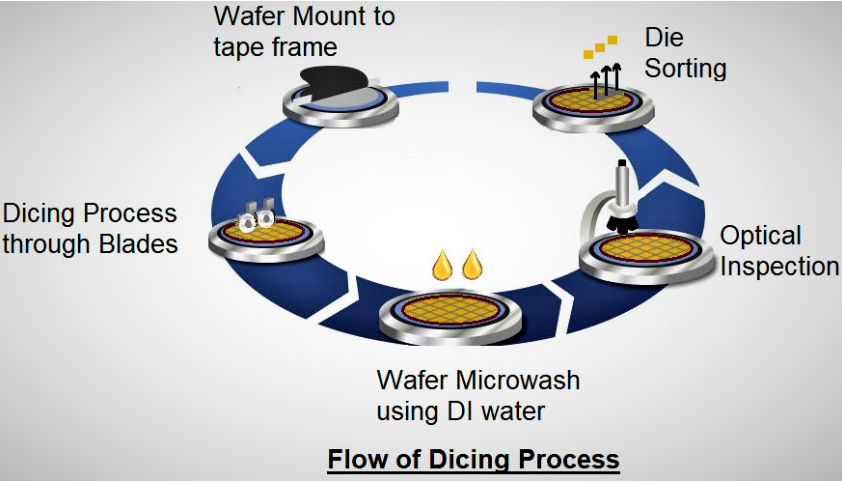
Фаза | Подробно описание |
Подготвителна фаза | -Почистване на вафлиИзползвайте вода с висока степен на пречистване и специализирани почистващи препарати, комбинирани с ултразвуково или механично почистване, за да премахнете примеси, частици и замърсители, осигурявайки чиста повърхност. -Прецизно позициониранеИзползвайте високопрецизно оборудване, за да осигурите точното разделяне на пластината по проектираните пътища на рязане. -Фиксиране на вафлиЗакрепете пластината върху рамка от лента, за да поддържате стабилност по време на рязане, предотвратявайки повреда от вибрации или движение. |
Фаза на рязане | -Нарязване на кубчета с остриеИзползвайте високоскоростни въртящи се диамантено покрити остриета за физическо рязане, подходящи за материали на силициева основа и рентабилни. -Лазерно нарязване на кубчетаИзползвайте високоенергийни лазерни лъчи за безконтактно рязане, идеални за крехки или високотвърди материали като галиев нитрид, предлагащи по-висока прецизност и по-малка загуба на материал. -Нови технологииВъвеждане на технологии за лазерно и плазмено рязане за допълнително подобряване на ефективността и прецизността, като същевременно се минимизират зоните, засегнати от топлина. |
Фаза на почистване | - Използвайте дейонизирана вода (DI вода) и специализирани почистващи препарати, комбинирани с ултразвуково или спрей почистване, за да премахнете отломките и праха, образувани по време на рязане, предотвратявайки евентуално повлияване на последващите процеси или електрическите характеристики на стружката от остатъци. - Високочистата деионизирана вода предотвратява навлизането на нови замърсители, осигурявайки чиста среда за пластините. |
Фаза на инспекция | -Оптична инспекцияИзползвайте оптични системи за откриване, комбинирани с алгоритми с изкуствен интелект, за бързо идентифициране на дефекти, като гарантирате липсата на пукнатини или отчупвания в нарязаните парченца, подобрявате ефективността на инспекцията и намалявате човешките грешки. -Измерване на размериПроверете дали размерите на чипа отговарят на проектните спецификации. -Тестване на електрическите характеристикиГарантиране на съответствие между електрическите характеристики на критичните чипове и стандартите, като по този начин се гарантира надеждност в последващи приложения. |
Фаза на сортиране | - Използвайте роботизирани рамена или вакуумни вендузи, за да отделите квалифицираните чипове от рамката на лентата и автоматично да ги сортирате въз основа на производителността, като по този начин осигурите ефективност и гъвкавост на производството, като същевременно подобрите прецизността. |
Процесът на рязане на пластини включва почистване, позициониране, рязане, почистване, инспекция и сортиране на пластините, като всяка стъпка е критична. С напредъка в автоматизацията, лазерното рязане и технологиите за инспекция с изкуствен интелект, съвременните системи за рязане на пластини могат да постигнат по-висока прецизност, скорост и по-ниски загуби на материал. В бъдеще новите технологии за рязане, като лазерно и плазмено, постепенно ще заменят традиционното рязане с остриета, за да отговорят на нуждите на все по-сложните дизайни на чипове, което допълнително ще стимулира развитието на процесите за производство на полупроводници.
Технология за рязане на пластини и нейните принципи
Изображението илюстрира три често срещани технологии за рязане на пластини:Нарязване на кубчета с острие,Лазерно нарязване на кубчетаиПлазмено нарязванеПо-долу е даден подробен анализ и допълнително обяснение на тези три техники:
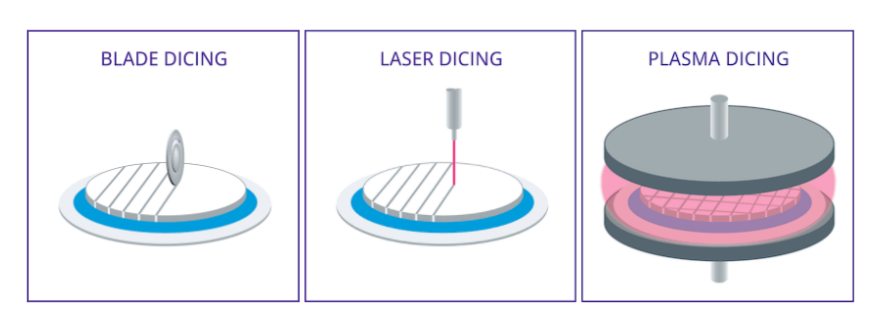
В производството на полупроводници, рязането на пластини е ключова стъпка, която изисква избор на подходящ метод за рязане въз основа на дебелината на пластината. Първата стъпка е да се определи дебелината на пластината. Ако дебелината на пластината надвишава 100 микрона, може да се избере метод на рязане с острие. Ако рязането с острие не е подходящо, може да се използва методът на рязане с фрактура, който включва както техники за рязане с рязане с драскотина, така и техники за рязане с острие.
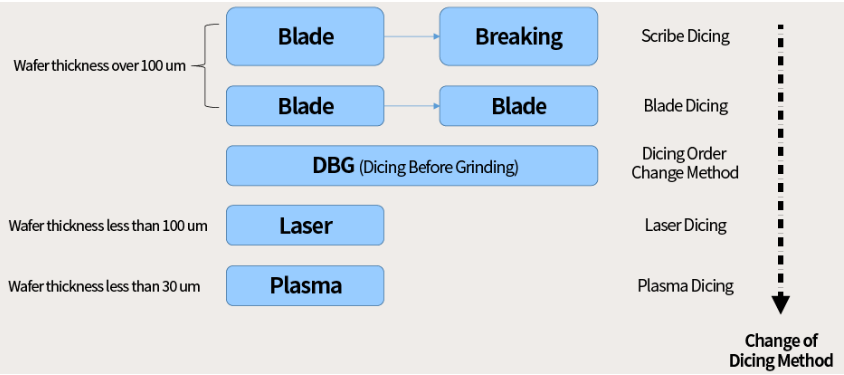
Когато дебелината на пластината е между 30 и 100 микрона, се препоръчва методът DBG (Dice Before Grinding). В този случай може да се избере рязане с чертане, рязане с острие или регулиране на последователността на рязане, ако е необходимо, за постигане на най-добри резултати.
За ултратънки пластини с дебелина по-малка от 30 микрона, лазерното рязане се превръща в предпочитан метод поради способността му да реже тънки пластини прецизно, без да причинява прекомерни повреди. Ако лазерното рязане не може да отговори на специфични изисквания, плазменото рязане може да се използва като алтернатива. Тази блок-схема предоставя ясен път за вземане на решения, за да се гарантира, че е избрана най-подходящата технология за рязане на пластини при различни условия на дебелина.
2.1 Технология за механично рязане
Технологията за механично рязане е традиционният метод за нарязване на пластини. Основният принцип е използването на високоскоростно въртящ се диамантен шлифовъчен диск като режещ инструмент за нарязване на пластината. Ключовото оборудване включва шпиндел с въздушен лагер, който задвижва диамантения шлифовъчен диск с високи скорости, за да извършва прецизно рязане или нарязване на канали по предварително определен път на рязане. Тази технология се използва широко в индустрията поради ниската си цена, високата ефективност и широката си приложимост.
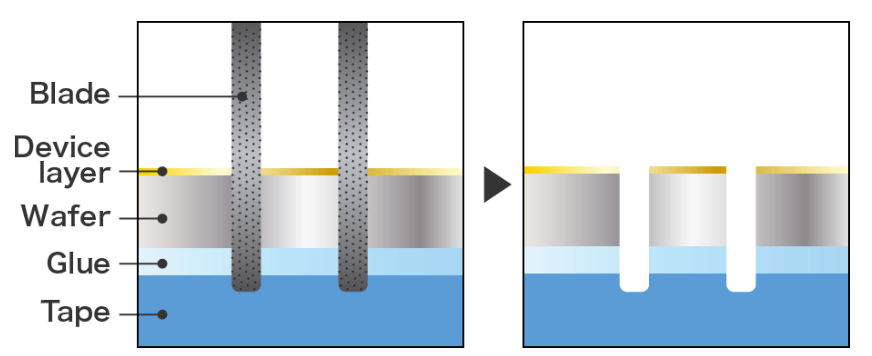
Предимства
Високата твърдост и износоустойчивост на диамантените шлифовъчни дискове позволяват на технологията за механично рязане да се адаптира към нуждите от рязане на различни материали за пластини, независимо дали става въпрос за традиционни материали на силициева основа или по-нови съставни полупроводници. Работата с нея е проста, с относително ниски технически изисквания, което допълнително насърчава популярността ѝ в масовото производство. Освен това, в сравнение с други методи за рязане, като лазерно рязане, механичното рязане има по-контролируеми разходи, което го прави подходящо за нуждите на производството с голям обем.
Ограничения
Въпреки многобройните си предимства, технологията за механично рязане има и ограничения. Първо, поради физическия контакт между инструмента и пластината, прецизността на рязане е относително ограничена, което често води до отклонения в размерите, които могат да повлияят на точността на последващото опаковане и тестване на чипа. Второ, дефекти като отчупване и пукнатини могат лесно да възникнат по време на процеса на механично рязане, което не само влияе върху добива, но може да повлияе негативно и на надеждността и живота на чиповете. Повредите, причинени от механично напрежение, са особено вредни за производството на чипове с висока плътност, особено при рязане на крехки материали, където тези проблеми са по-изразени.
Технологични подобрения
За да преодолеят тези ограничения, изследователите непрекъснато оптимизират процеса на механично рязане. Ключовите подобрения включват подобряване на дизайна и избора на материали за шлифовъчните дискове, за да се подобри прецизността и издръжливостта на рязане. Освен това, оптимизирането на структурния дизайн и системите за управление на режещото оборудване допълнително подобри стабилността и автоматизацията на процеса на рязане. Тези подобрения намаляват грешките, причинени от човешки операции, и подобряват постоянството на разрезите. Въвеждането на усъвършенствани технологии за инспекция и контрол на качеството за наблюдение в реално време на аномалии по време на процеса на рязане също значително подобри надеждността и добива на рязане.
Бъдещо развитие и нови технологии
Въпреки че технологията за механично рязане все още заема значителна позиция в рязането на пластини, новите технологии за рязане се развиват бързо с развитието на полупроводниковите процеси. Например, прилагането на технология за термично лазерно рязане предоставя нови решения за проблемите с прецизността и дефектите при механичното рязане. Този безконтактен метод на рязане намалява физическото напрежение върху пластината, като значително намалява честотата на отчупване и напукване, особено при рязане на по-крехки материали. В бъдеще интегрирането на технологията за механично рязане с новите техники за рязане ще осигури на производството на полупроводници повече възможности и гъвкавост, като допълнително подобри ефективността на производството и качеството на чиповете.
В заключение, въпреки че технологията за механично рязане има определени недостатъци, непрекъснатите технологични подобрения и интегрирането ѝ с нови техники за рязане ѝ позволяват да продължи да играе важна роля в производството на полупроводници и да поддържа конкурентоспособността си в бъдещите процеси.
2.2 Технология за лазерно рязане
Технологията за лазерно рязане, като нов метод за рязане на пластини, постепенно придоби широко внимание в полупроводниковата индустрия поради високата си прецизност, липсата на механични контактни повреди и възможностите за бързо рязане. Тази технология използва високата енергийна плътност и фокусиращата способност на лазерния лъч, за да създаде малка зона, засегната от топлина, върху повърхността на материала на пластината. Когато лазерният лъч се приложи върху пластината, генерираното термично напрежение кара материала да се разчупи на определеното място, постигайки прецизно рязане.
Предимства на технологията за лазерно рязане
• Висока прецизностПрецизната способност за позициониране на лазерния лъч позволява прецизност на рязане на микронно или дори нанометрово ниво, отговаряйки на изискванията на съвременното високопрецизно производство на интегрални схеми с висока плътност.
• Без механичен контактЛазерното рязане избягва физически контакт с пластината, предотвратявайки често срещани проблеми при механичното рязане, като например отчупване и напукване, значително подобрявайки добива и надеждността на чиповете.
• Бърза скорост на рязанеВисоката скорост на лазерното рязане допринася за повишена ефективност на производството, което го прави особено подходящ за мащабни, високоскоростни производствени сценарии.
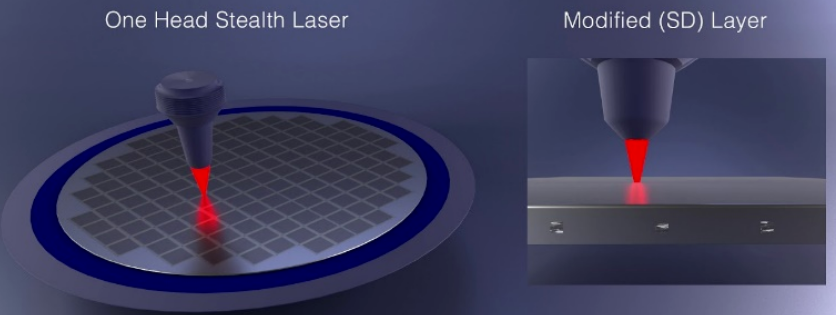
Предизвикателства, пред които сме изправени
• Висока цена на оборудванетоПървоначалната инвестиция за оборудване за лазерно рязане е висока, което представлява икономически натиск, особено за малките и средни производствени предприятия.
• Сложно управление на процеситеЛазерното рязане изисква прецизен контрол на няколко параметъра, включително плътност на енергията, позиция на фокуса и скорост на рязане, което прави процеса сложен.
• Проблеми със засегнатите от топлината зониВъпреки че безконтактният характер на лазерното рязане намалява механичните повреди, термичното напрежение, причинено от зоната, засегната от топлината (HAZ), може да повлияе негативно върху свойствата на материала на пластината. Необходима е допълнителна оптимизация на процеса, за да се сведе до минимум този ефект.
Насоки за технологично подобрение
За да се справят с тези предизвикателства, изследователите се фокусират върху намаляване на разходите за оборудване, подобряване на ефективността на рязане и оптимизиране на технологичния процес.
• Ефективни лазери и оптични системиЧрез разработването на по-ефективни лазери и усъвършенствани оптични системи е възможно да се намалят разходите за оборудване, като същевременно се подобри прецизността и скоростта на рязане.
• Оптимизиране на параметрите на процесаПровеждат се задълбочени изследвания на взаимодействието между лазерите и материалите за пластини, за да се подобрят процесите, които намаляват зоната, засегната от топлина, като по този начин се подобрява качеството на рязане.
• Интелигентни системи за управлениеРазработването на интелигентни технологии за управление има за цел да автоматизира и оптимизира процеса на лазерно рязане, подобрявайки неговата стабилност и постоянство.
Технологията за лазерно рязане е особено ефективна при ултратънки пластини и сценарии за високопрецизно рязане. С увеличаването на размерите на пластините и нарастването на плътността на схемите, традиционните методи за механично рязане трудно успяват да отговорят на изискванията за висока прецизност и висока ефективност на съвременното производство на полупроводници. Поради уникалните си предимства, лазерното рязане се превръща в предпочитано решение в тези области.
Въпреки че технологията за лазерно рязане все още е изправена пред предизвикателства като високи разходи за оборудване и сложност на процеса, нейните уникални предимства по отношение на висока прецизност и безконтактно увреждане я правят важна насока за развитие в производството на полупроводници. С развитието на лазерните технологии и интелигентните системи за управление се очаква лазерното рязане допълнително да подобри ефективността и качеството на рязане на пластини, което ще стимулира непрекъснатото развитие на полупроводниковата индустрия.
2.3 Технология за плазмено рязане
Технологията за плазмено рязане, като нововъзникващ метод за нарязване на пластини, привлече значително внимание през последните години. Тази технология използва високоенергийни плазмени лъчи за прецизно рязане на пластини, като контролира енергията, скоростта и пътя на рязане на плазмения лъч, постигайки оптимални резултати от рязането.
Принцип на работа и предимства
Процесът на плазмено рязане разчита на високотемпературен, високоенергиен плазмен лъч, генериран от оборудването. Този лъч може да нагрее материала на пластината до точката му на топене или изпаряване за много кратко време, което позволява бързо рязане. В сравнение с традиционното механично или лазерно рязане, плазменото рязане е по-бързо и създава по-малка зона на топлинно въздействие, което ефективно намалява появата на пукнатини и повреди по време на рязане.
В практически приложения, технологията за плазмено рязане е особено подходяща за работа с пластини със сложни форми. Нейният високоенергиен, регулируем плазмен лъч може лесно да реже пластини с неправилна форма с висока прецизност. Следователно, в производството на микроелектроника, особено при персонализирано и дребносерийно производство на висок клас чипове, тази технология е многообещаваща за широко приложение.
Предизвикателства и ограничения
Въпреки многобройните предимства на технологията за плазмено рязане, тя е изправена и пред някои предизвикателства.
• Сложен процесПроцесът на плазмено рязане е сложен и изисква високопрецизно оборудване и опитни оператори, за да се гарантираточност и стабилност при рязане.
• Контрол на околната среда и безопасностВисокотемпературният и високоенергиен характер на плазмения лъч изисква строг контрол на околната среда и мерки за безопасност, което увеличава сложността и разходите за внедряване.
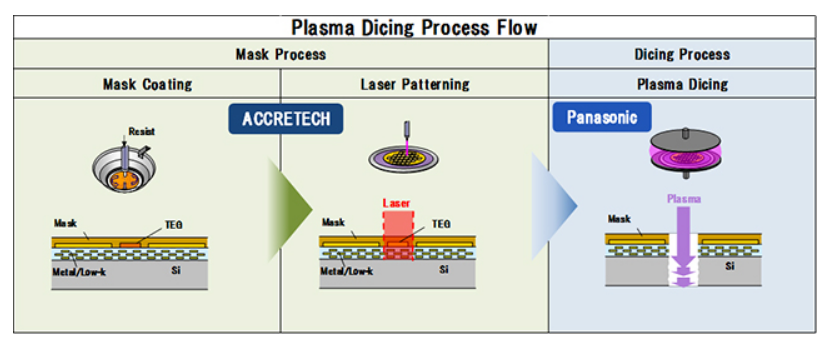
Бъдещи насоки за развитие
С технологичния напредък се очаква предизвикателствата, свързани с плазменото рязане, постепенно да бъдат преодолени. Чрез разработването на по-интелигентно и по-стабилно оборудване за рязане може да се намали зависимостта от ръчни операции, като по този начин се подобри ефективността на производството. В същото време, оптимизирането на параметрите на процеса и средата за рязане ще спомогне за намаляване на рисковете за безопасността и оперативните разходи.
В полупроводниковата индустрия иновациите в технологиите за рязане и нарязване на пластини са от решаващо значение за развитието ѝ. Технологията за плазмено рязане, с високата си прецизност, ефективност и способност за обработка на сложни форми на пластини, се очертава като значителен нов играч в тази област. Въпреки че някои предизвикателства остават, те ще бъдат постепенно решени с продължаващи технологични иновации, носейки повече възможности за производството на полупроводници.
Перспективите за приложение на технологията за плазмено рязане са огромни и се очаква тя да играе все по-важна роля в производството на полупроводници в бъдеще. Чрез непрекъснати технологични иновации и оптимизация, плазменото рязане не само ще се справи със съществуващите предизвикателства, но и ще се превърне в мощен двигател на растежа на полупроводниковата индустрия.
2.4 Качество на рязане и фактори, влияещи върху него
Качеството на рязане на пластини е от решаващо значение за последващото опаковане на чиповете, тестване и цялостната производителност и надеждност на крайния продукт. Често срещани проблеми, срещани по време на рязане, включват пукнатини, отчупване и отклонения при рязане. Тези проблеми се влияят от няколко фактора, действащи заедно.
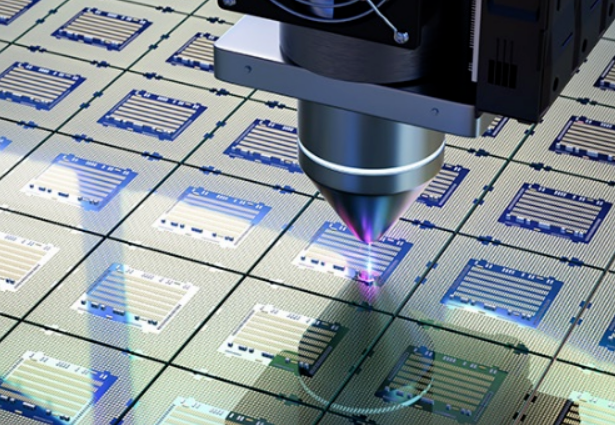
Категория | Съдържание | Въздействие |
Параметри на процеса | Скоростта на рязане, подаването и дълбочината на рязане влияят пряко върху стабилността и прецизността на процеса на рязане. Неправилните настройки могат да доведат до концентрация на напрежение и прекомерна зона, засегната от топлина, което води до пукнатини и отчупване. Подходящото регулиране на параметрите въз основа на материала на пластината, дебелината и изискванията за рязане е ключово за постигане на желаните резултати от рязането. | Правилните параметри на процеса осигуряват прецизно рязане и намаляват риска от дефекти като пукнатини и отчупване. |
Фактори, свързани с оборудването и материалите | -Качество на остриетоМатериалът, твърдостта и износоустойчивостта на острието влияят върху гладкостта на процеса на рязане и плоскостта на режещата повърхност. Остриетата с лошо качество увеличават триенето и термичното напрежение, което потенциално води до пукнатини или отчупване. Изборът на правилния материал за острието е от решаващо значение. -Производителност на охлаждащата течностОхлаждащите течности помагат за намаляване на температурата на рязане, минимизиране на триенето и отстраняване на отломки. Неефективната охлаждаща течност може да доведе до високи температури и натрупване на отломки, което да повлияе на качеството и ефективността на рязане. Изборът на ефикасни и екологични охлаждащи течности е жизненоважен. | Качеството на острието влияе върху прецизността и гладкостта на рязането. Неефективната охлаждаща течност може да доведе до лошо качество и ефективност на рязането, което подчертава необходимостта от оптимално използване на охлаждащата течност. |
Контрол на процесите и проверка на качеството | -Контрол на процеситеМониторинг в реално време и регулиране на ключови параметри на рязане, за да се осигури стабилност и постоянство в процеса на рязане. -Инспекция на качествотоПроверките на външния вид след рязане, измерванията на размерите и тестовете за електрически характеристики помагат за бързото идентифициране и отстраняване на проблеми с качеството, подобрявайки точността и постоянството на рязането. | Правилният контрол на процеса и проверката на качеството спомагат за осигуряване на постоянни, висококачествени резултати от рязането и ранно откриване на потенциални проблеми. |

Подобряване на качеството на рязане
Подобряването на качеството на рязане изисква цялостен подход, който отчита параметрите на процеса, избора на оборудване и материали, контрола на процеса и инспекцията. Чрез непрекъснато усъвършенстване на технологиите за рязане и оптимизиране на методите на процеса, прецизността и стабилността на рязането на пластини могат да бъдат допълнително подобрени, осигурявайки по-надеждна техническа поддръжка за индустрията за производство на полупроводници.
#03 Обработка и тестване след рязане
3.1 Почистване и сушене
Етапите на почистване и сушене след рязане на пластината са от решаващо значение за осигуряване на качеството на чипа и безпроблемното протичане на последващите процеси. По време на този етап е важно да се отстранят старателно силициевите отломки, остатъците от охлаждаща течност и други замърсители, образувани по време на рязането. Също толкова важно е да се гарантира, че чиповете не са повредени по време на процеса на почистване и след изсушаване да се гарантира, че по повърхността на чипа не е останала влага, за да се предотвратят проблеми като корозия или електростатичен разряд.
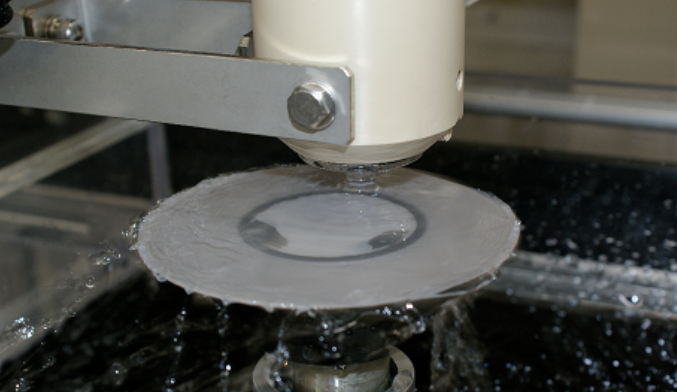
Обработка след рязане: Процес на почистване и сушене
Стъпка на процеса | Съдържание | Въздействие |
Процес на почистване | -МетодИзползвайте специализирани почистващи препарати и чиста вода, комбинирани с ултразвукови или механични техники за почистване с четка. | Осигурява цялостно отстраняване на замърсители и предотвратява повреда на стружките по време на почистване. |
-Избор на почистващ препаратИзберете въз основа на материала на пластината и вида на замърсителя, за да осигурите ефективно почистване без повреждане на чипа. | Правилният избор на препарат е ключов за ефективното почистване и защита от стружки. | |
-Контрол на параметритеСтриктно контролирайте температурата, времето и концентрацията на почистващия разтвор, за да предотвратите проблеми с качеството, причинени от неправилно почистване. | Контролите помагат да се избегне повреждане на пластината или оставяне на замърсители, осигурявайки постоянно качество. | |
Процес на сушене | -Традиционни методиЕстествено сушене на въздух и сушене с горещ въздух, които са с ниска ефективност и могат да доведат до натрупване на статично електричество. | Може да доведе до по-бавно време за съхнене и потенциални проблеми със статичното електричество. |
-Модерни технологииИзползвайте съвременни технологии като вакуумно сушене и инфрачервено сушене, за да осигурите бързо изсъхване на чипса и да избегнете вредни ефекти. | По-бърз и по-ефективен процес на сушене, намаляващ риска от статично електричество или проблеми, свързани с влага. | |
Избор и поддръжка на оборудване | -Избор на оборудванеВисокопроизводителните машини за почистване и сушене подобряват ефективността на обработката и прецизно контролират потенциалните проблеми по време на работа. | Висококачествените машини осигуряват по-добра обработка и намаляват вероятността от грешки по време на почистване и сушене. |
-Поддръжка на оборудванеРедовната проверка и поддръжка на оборудването гарантират оптималното му работно състояние, гарантирайки качеството на стружките. | Правилната поддръжка предотвратява повреди на оборудването, осигурявайки надеждна и висококачествена обработка. |
Почистване и сушене след рязане
Етапите на почистване и сушене след рязане на пластини са сложни и деликатни процеси, които изискват внимателно обмисляне на множество фактори, за да се гарантира крайният резултат от обработката. Чрез използването на научни методи и строги процедури е възможно да се гарантира, че всеки чип влиза в следващите етапи на опаковане и тестване в оптимално състояние.
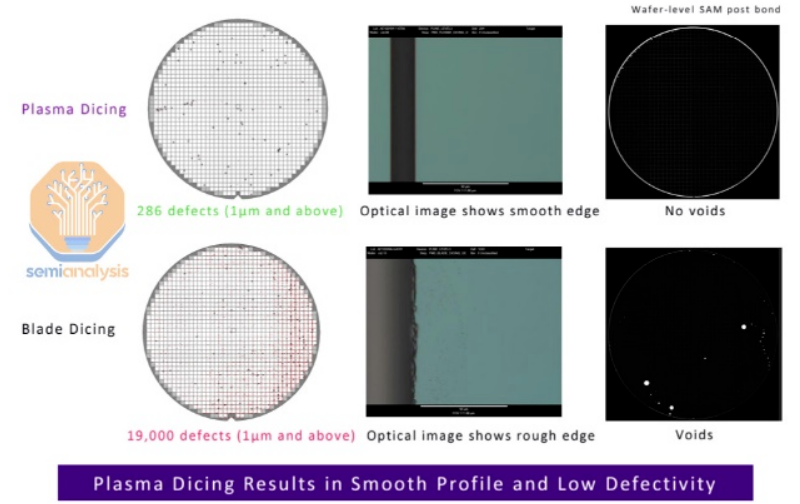
Инспекция и тестване след рязане
Стъпка | Съдържание | Въздействие |
Стъпка на инспекция | 1.Визуална проверкаИзползвайте визуално или автоматизирано оборудване за проверка, за да проверите за видими дефекти като пукнатини, отчупвания или замърсяване на повърхността на чипа. Бързо идентифицирайте физически повредените чипове, за да избегнете разхищение. | Помага за идентифициране и елиминиране на дефектни стружки в ранен етап на процеса, намалявайки загубата на материал. |
2.Измерване на размераИзползвайте прецизни измервателни устройства, за да измерите точно размерите на чипа, като гарантирате, че размерът на рязането отговаря на проектните спецификации и предотвратявате проблеми с производителността или трудности при опаковането. | Гарантира, че чиповете са в рамките на необходимите граници на размера, предотвратявайки влошаване на производителността или проблеми със сглобяването. | |
3.Тестване на електрическите характеристикиОценете ключови електрически параметри като съпротивление, капацитет и индуктивност, за да идентифицирате несъвместими чипове и да гарантирате, че само чипове с подходяща производителност преминават към следващия етап. | Гарантира, че в процеса се използват само функционални и тествани за производителност чипове, намалявайки риска от повреда в по-късни етапи. | |
Стъпка на тестване | 1.Функционално тестванеПроверка: Проверка дали основната функционалност на чипа работи по предназначение, идентифициране и елиминиране на чипове с функционални аномалии. | Гарантира, че чиповете отговарят на основните оперативни изисквания, преди да преминат към по-късни етапи. |
2.Тестване на надеждносттаОценка на стабилността на производителността на чипа при продължителна употреба или в тежки условия, обикновено включващи стареене при висока температура, тестване при ниска температура и тестване за влажност, за да се симулират екстремни условия в реални условия. | Гарантира надеждното функциониране на чиповете при различни условия на околната среда, подобрявайки дълготрайността и стабилността на продукта. | |
3.Тестване за съвместимостПроверете дали чипът работи правилно с други компоненти или системи, като се уверите, че няма повреди или влошаване на производителността поради несъвместимост. | Осигурява безпроблемна работа в реални приложения, като предотвратява проблеми със съвместимостта. |
3.3 Опаковка и съхранение
След рязане на пластини, чиповете са ключов продукт от производствения процес на полупроводници, а етапите на тяхното опаковане и съхранение са също толкова важни. Правилните мерки за опаковане и съхранение са от съществено значение не само за осигуряване на безопасността и стабилността на чиповете по време на транспортиране и съхранение, но и за осигуряване на силна поддръжка за последващите етапи на производство, тестване и опаковане.
Обобщение на етапите на инспекция и тестване:
Стъпките за проверка и тестване на чипове след рязане на пластини обхващат редица аспекти, включително визуална проверка, измерване на размера, тестване на електрическите характеристики, функционално тестване, тестване на надеждността и тестване за съвместимост. Тези стъпки са взаимосвързани и допълващи се, образувайки солидна бариера за гарантиране на качеството и надеждността на продукта. Чрез строги процедури за проверка и тестване, потенциалните проблеми могат да бъдат идентифицирани и решени своевременно, като се гарантира, че крайният продукт отговаря на изискванията и очакванията на клиентите.
Аспект | Съдържание |
Мерки за опаковане | 1.АнтистатиченОпаковъчните материали трябва да имат отлични антистатични свойства, за да предотвратят повредата на устройствата или влиянието върху тяхната работа от статично електричество. |
2.ВлагоустойчивОпаковъчните материали трябва да имат добра устойчивост на влага, за да предотвратят корозия и влошаване на електрическите характеристики, причинени от влажност. | |
3.УдароустойчивОпаковъчните материали трябва да осигуряват ефективно поглъщане на удари, за да предпазят чиповете от вибрации и удари по време на транспортиране. | |
Среда за съхранение | 1.Контрол на влажносттаСтриктно контролирайте влажността в подходящ диапазон, за да предотвратите абсорбцията на влага и корозията, причинени от прекомерна влажност или статични проблеми, причинени от ниска влажност. |
2.ЧистотаПоддържайте чиста среда за съхранение, за да избегнете замърсяване на стружките с прах и примеси. | |
3.Контрол на температуратаЗадайте разумен температурен диапазон и поддържайте температурна стабилност, за да предотвратите ускорено стареене поради прекомерна топлина или проблеми с кондензацията, причинени от ниски температури. | |
Редовна инспекция | Редовно проверявайте и оценявайте съхраняваните чипове, като използвате визуални проверки, измервания на размери и тестове за електрически характеристики, за да идентифицирате и отстраните потенциални проблеми своевременно. Въз основа на времето и условията на съхранение планирайте употребата на чиповете, за да гарантирате, че те се използват в оптимално състояние. |
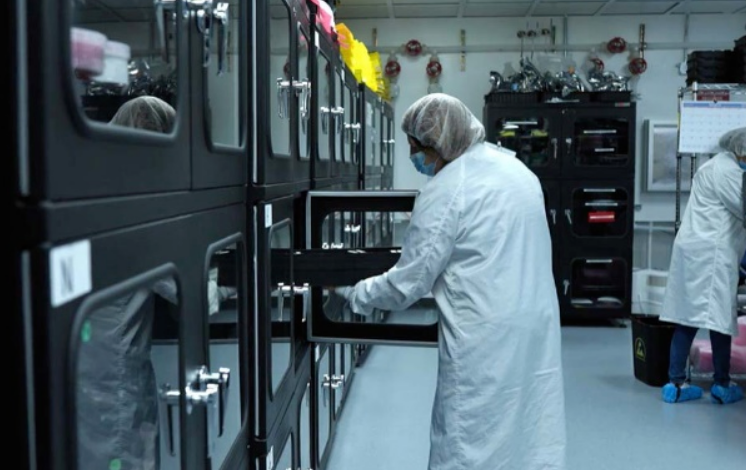
Проблемът с микропукнатините и повредите по време на процеса на нарязване на пластините е значително предизвикателство в производството на полупроводници. Напрежението при рязане е основната причина за това явление, тъй като създава малки пукнатини и повреди по повърхността на пластината, което води до увеличаване на производствените разходи и намаляване на качеството на продукта.
За да се справим с това предизвикателство, е изключително важно да се сведе до минимум напрежението при рязане и да се приложат оптимизирани техники, инструменти и условия на рязане. Внимателното внимание към фактори като материал на острието, скорост на рязане, налягане и методи на охлаждане може да помогне за намаляване на образуването на микропукнатини и да подобри общия добив на процеса. Освен това, текущите изследвания на по-модерни технологии за рязане, като например лазерно нарязване, проучват начини за по-нататъшно смекчаване на тези проблеми.
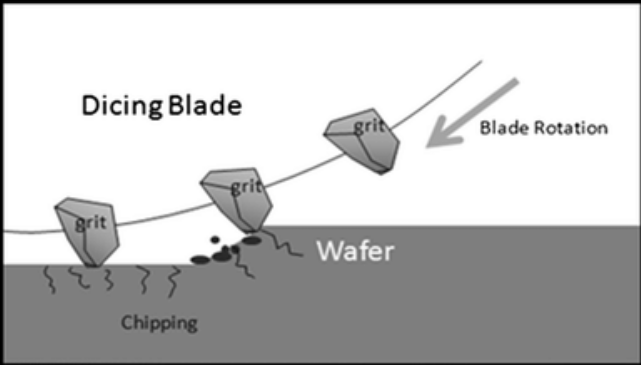
Като крехък материал, пластините са склонни към вътрешни структурни промени, когато са подложени на механично, термично или химическо натоварване, което води до образуването на микропукнатини. Въпреки че тези пукнатини може да не са веднага забележими, те могат да се разширят и да причинят по-сериозни повреди с напредването на производствения процес. Този проблем става особено проблематичен по време на последващите етапи на опаковане и тестване, където температурните колебания и допълнителните механични натоварвания могат да доведат до превръщането на тези микропукнатини във видими фрактури, което потенциално може да доведе до повреда на чипа.
За да се смекчи този риск, е важно процесът на рязане да се контролира внимателно чрез оптимизиране на параметри като скорост на рязане, налягане и температура. Използването на по-малко агресивни методи за рязане, като лазерно нарязване, може да намали механичното напрежение върху пластината и да сведе до минимум образуването на микропукнатини. Освен това, прилагането на усъвършенствани методи за проверка, като инфрачервено сканиране или рентгеново изображение по време на процеса на нарязване на пластината, може да помогне за откриването на тези пукнатини в ранен етап, преди да причинят по-нататъшни щети.
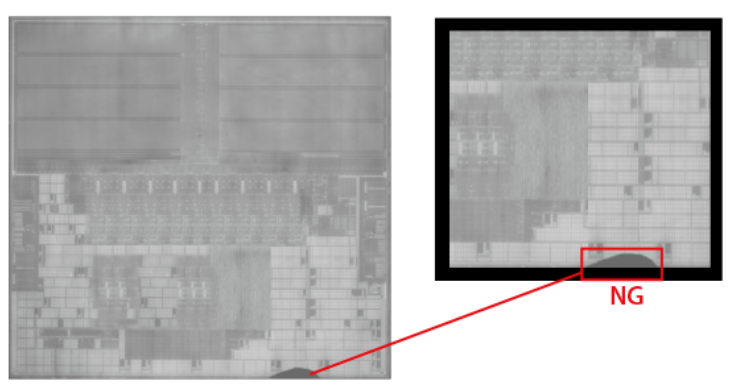
Повредата на повърхността на пластината е сериозен проблем в процеса на нарязване, тъй като може да има пряко въздействие върху производителността и надеждността на чипа. Такива повреди могат да бъдат причинени от неправилна употреба на режещи инструменти, неправилни параметри на рязане или дефекти на материала, присъщи на самата пластина. Независимо от причината, тези повреди могат да доведат до промени в електрическото съпротивление или капацитета на веригата, което влияе върху цялостната производителност.
За справяне с тези проблеми се проучват две ключови стратегии:
1. Оптимизиране на режещи инструменти и параметриЧрез използване на по-остри остриета, регулиране на скоростта на рязане и промяна на дълбочината на рязане, концентрацията на напрежение по време на процеса на рязане може да бъде сведена до минимум, като по този начин се намалява потенциалът за повреда.
2. Изследване на нови технологии за рязанеУсъвършенствани техники като лазерно рязане и плазмено рязане предлагат подобрена прецизност, като същевременно потенциално намаляват нивото на повреди, нанесени на пластината. Тези технологии се изучават, за да се намерят начини за постигане на висока точност на рязане, като същевременно се минимизира термичното и механичното напрежение върху пластината.
Площ на термично въздействие и нейното влияние върху производителността
При термични процеси на рязане, като лазерно и плазмено рязане, високите температури неизбежно създават зона на термично въздействие върху повърхността на пластината. Тази област, където температурният градиент е значителен, може да промени свойствата на материала, което да повлияе на крайните характеристики на чипа.
Въздействие на термично засегнатата зона (TAZ):
Промени в кристалната структураПри високи температури атомите в материала на пластината могат да се пренаредят, причинявайки нарушения в кристалната структура. Това изкривяване отслабва материала, намалявайки неговата механична якост и стабилност, което увеличава риска от повреда на чипа по време на употреба.
Промени в електрическите свойстваВисоките температури могат да променят концентрацията и мобилността на носителите в полупроводниковите материали, което влияе върху електрическата проводимост на чипа и ефективността на токопренос. Тези промени могат да доведат до спад в производителността на чипа, което потенциално го прави негоден за предназначението му.
За да се смекчат тези ефекти, контролирането на температурата по време на рязане, оптимизирането на параметрите на рязане и проучването на методи като охлаждащи струи или последваща обработка са основни стратегии за намаляване на степента на термично въздействие и поддържане на целостта на материала.
Като цяло, както микропукнатините, така и зоните на термичен удар са ключови предизвикателства в технологията за нарязване на пластини. Необходими са непрекъснати изследвания, наред с технологичния напредък и мерките за контрол на качеството, за да се подобри качеството на полупроводниковите продукти и да се повиши тяхната пазарна конкурентоспособност.
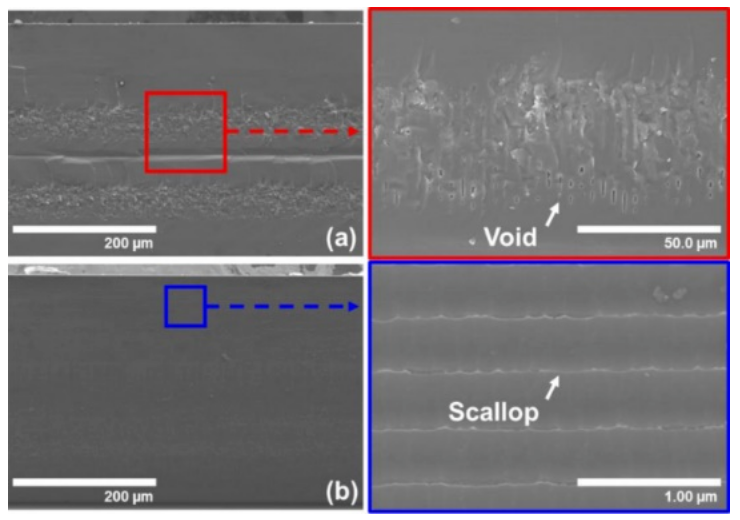
Мерки за контрол на зоната на термично въздействие:
Оптимизиране на параметрите на процеса на рязанеНамаляването на скоростта и мощността на рязане може ефективно да минимизира размера на зоната на термично въздействие (TAZ). Това помага за контролиране на количеството топлина, генерирано по време на процеса на рязане, което пряко влияе върху свойствата на материала на пластината.
Усъвършенствани технологии за охлажданеПрилагането на технологии като охлаждане с течен азот и микрофлуидно охлаждане може значително да ограничи обхвата на зоната на термично въздействие. Тези методи на охлаждане спомагат за по-ефективното разсейване на топлината, като по този начин запазват материалните свойства на пластината и минимизират термичните повреди.
Избор на материалИзследователите изследват нови материали, като въглеродни нанотръби и графен, които притежават отлична топлопроводимост и механична якост. Тези материали могат да намалят зоната на термично въздействие, като същевременно подобрят цялостната производителност на чиповете.
В обобщение, въпреки че зоната на термично въздействие е неизбежна последица от технологиите за термично рязане, тя може да бъде ефективно контролирана чрез оптимизирани техники за обработка и избор на материали. Бъдещите изследвания вероятно ще се фокусират върху фина настройка и автоматизиране на процесите на термично рязане, за да се постигне по-ефективно и прецизно нарязване на пластини.

Стратегия за баланс:
Постигането на оптимален баланс между добива на вафли и ефективността на производството е постоянно предизвикателство в технологията за нарязване на вафли. Производителите трябва да вземат предвид множество фактори, като пазарно търсене, производствени разходи и качество на продукта, за да разработят рационална производствена стратегия и параметри на процеса. В същото време, въвеждането на усъвършенствано оборудване за рязане, подобряването на уменията на операторите и подобряването на контрола върху качеството на суровините са от съществено значение за поддържане или дори подобряване на добива, като същевременно се увеличава ефективността на производството.
Бъдещи предизвикателства и възможности:
С напредъка на полупроводниковите технологии, рязането на пластини е изправено пред нови предизвикателства и възможности. С намаляването на размерите на чиповете и увеличаването на интеграцията, изискванията за прецизност и качество на рязане нарастват значително. Едновременно с това, нововъзникващите технологии предоставят нови идеи за разработване на техники за рязане на пластини. Производителите трябва да са в крак с пазарната динамика и технологичните тенденции, като непрекъснато коригират и оптимизират производствените стратегии и параметрите на процеса, за да отговорят на пазарните промени и технологичните изисквания.
В заключение, чрез интегриране на съображения за пазарно търсене, производствени разходи и качество на продукта, както и чрез въвеждане на съвременно оборудване и технологии, подобряване на уменията на операторите и засилване на контрола върху суровините, производителите могат да постигнат най-добрия баланс между добива на пластини и ефективността на производството по време на нарязването на пластини, което води до ефективно и висококачествено производство на полупроводникови продукти.
Бъдещи перспективи:
С бързия технологичен напредък, полупроводниковата технология се развива с безпрецедентни темпове. Като критична стъпка в производството на полупроводници, технологията за рязане на пластини е готова за вълнуващи нови разработки. В бъдеще се очаква технологията за рязане на пластини да постигне значителни подобрения в прецизността, ефективността и разходите, вдъхвайки нов тласък на непрекъснатия растеж на полупроводниковата индустрия.
Повишаване на прецизността:
В стремежа си към по-висока прецизност, технологията за рязане на пластини непрекъснато ще разширява границите на съществуващите процеси. Чрез задълбочено изучаване на физичните и химичните механизми на процеса на рязане и прецизен контрол на параметрите на рязане, ще се постигнат по-фини резултати от рязането, за да се отговорят на все по-сложните изисквания за проектиране на схеми. Освен това, изследването на нови материали и методи за рязане значително ще подобри добива и качеството.
Повишаване на ефективността:
Новото оборудване за рязане на пластини ще се фокусира върху интелигентен и автоматизиран дизайн. Въвеждането на усъвършенствани системи за управление и алгоритми ще позволи на оборудването автоматично да регулира параметрите на рязане, за да отговаря на различни материали и изисквания за дизайн, като по този начин значително ще подобри ефективността на производството. Иновации като технология за рязане на множество пластини и системи за бърза смяна на остриетата ще играят ключова роля за повишаване на ефективността.
Намаляване на разходите:
Намаляването на разходите е ключова насока за развитието на технологията за рязане на пластини. С разработването на нови материали и методи за рязане се очаква разходите за оборудване и поддръжка да бъдат ефективно контролирани. Освен това, оптимизирането на производствените процеси и намаляването на процента на брак ще намали допълнително отпадъците по време на производството, което ще доведе до намаляване на общите производствени разходи.
Интелигентно производство и Интернет на нещата:
Интеграцията на интелигентното производство и технологиите за интернет на нещата (IoT) ще донесе трансформативни промени в технологията за рязане на пластини. Чрез взаимосвързаност и споделяне на данни между устройствата, всяка стъпка от производствения процес може да бъде наблюдавана и оптимизирана в реално време. Това не само подобрява ефективността на производството и качеството на продуктите, но и предоставя на компаниите по-точни пазарни прогнози и подкрепа при вземане на решения.
В бъдеще технологията за рязане на пластини ще постигне забележителен напредък в прецизността, ефективността и разходите. Тези постижения ще стимулират непрекъснатото развитие на полупроводниковата индустрия и ще донесат повече технологични иновации и удобства на човешкото общество.
Време на публикуване: 19 ноември 2024 г.